Carrier Chiller Manual 23xl Screw
Installation Instructions SAFETY CONSIDERATIONS Screw liquid chillers are designed to provide safe and re- liable service when operated within design specifica- tions. When operating this equipment, use good judgment and follow safety precautions to avoid damage to equip- ment and property or injury to personnel. Be sure you understand and follow the procedures and safety precautions contained in the machine instruc- tions as well as those listed in this guide. DO NOT VENT refrigerant relief devices within a building.
Outlet from rupture disc or relief valve must be vented outdoors in ac- cordance with the latest edition of ANSI/ASHRAE 15 (American National Standards Institute/American Society of Heating, Refrigeration, and Air Conditioning Engineers). The accumulation of refrigerant in an enclosed space can displace oxygen and cause asphyxiation. PROVIDE adequate ventilation in accordance with ANSI/ASHRAE 15, especially for enclosed and low overhead spaces. Inhalation of high concentrations of vapor is harmful and may cause heart ir- regularities, unconsciousness, or death. Intentional misuse can be fatal. Vapor is heavier than air and reduces the amount of oxygen available for breathing.
Carrier 23XL Installation Instructions Manual. Hermetic Screw Liquid Chillers. With HCFC-22 and HFC-134a. I am aware that the start-up time for a Carrier chiller can take between 2 and 6 days depending on the model of the machine and the options and accessories used with it. Manager III (CSM III). The CHILLERVISOR System Manager III (part number. Functions to optimize the efficiency of your Carrier chiller plant. 23XL screw type. 30 GX/HX screw type. Specifications subject to change without notice.
Product causes eye and skin irritation. De- composition products are hazardous. DO NOT USE OXYGEN to purge lines or to pressurize a machine for any purpose. Oxygen gas reacts violently with oil, grease, and other common substances. DO NOT USE air to leak test.
Use only refrigerant or dry nitrogen. NEVER EXCEED specified test pressures. VERIFY the allowable test pressure by checking the instruction literature and the design pressures on the equipment nameplate. DO NOT VALVE OFF any safety device. BE SURE that all pressure relief devices are properly installed and functioning before operating any machine.
DO NOT WELD OR FLAMECUT any refrigerant line or vessel until all refrigerant (liquid and vapor) has been removed from chiller. Traces of vapor should be displaced with dry air or nitrogen and the work area should be well ventilated. Refrigerant in contact with an open flame produces toxic gases. DO NOT USE eyebolts or eyebolt holes to rig machine sections or the entire assembly.
DO NOT work on high-voltage equipment unless you are a quali- fied electrician. DO NOT WORK ON electrical components, including control center, switches, starters, or oil heater until you are sure ALL POWER IS OFF and no residual voltage can leak from capacitors or solid- state components. LOCK OPEN AND TAG electrical circuits during servicing. IF WORK IS INTERRUPTED, confirm that all circuits are deenergized be- fore resuming work. DO NOT syphon refrigerant. AVOID SPILLING liquid refrigerant on skin or getting it into the eyes. USE SAFETY GOGGLES.
Wash any spills from the skin with soap and water. If liquid refrigerant enters the eyes, IMME- DIATELY FLUSH EYES with water and consult a physician. NEVER APPLY an open flame or live steam to a refrigerant cylinder. Dangerous over pressure can result. When it is necessary to heat refrigerant, use only warm (110 F 43 C) water. DO NOT REUSE disposable (nonreturnable) cylinders or attempt to refill them. It is DANGEROUS AND ILLEGAL.
When cylinder is emptied, evacuate remaining gas pressure, loosen the collar, and unscrew and discard the valve stem. DO NOT INCINERATE. CHECK THE REFRIGERANT TYPE before adding refrigerant to the machine. The introduction of the wrong refrigerant can cause machine damage or malfunction. Operation of this equipment with refrigerants other than those cited herein should comply with ANSI/ASHRAE-15 (latest edition).
Contact Carrier for further information on use of this machine with other refrigerants. DO NOT ATTEMPT TO REMOVE fittings, covers, etc., while ma- chine is under pressure or while machine is running. Be sure pres- sure is at 0 psig (0 kPa) before breaking any refrigerant connection. CAREFULLY INSPECT all relief valves, rupture discs, and other relief devices AT LEAST ONCE A YEAR. If machine operates in a corrosive atmosphere, inspect the devices at more frequent intervals.
DO NOT ATTEMPT TO REPAIR OR RECONDITION any relief valve when corrosion or build-up of foreign material (rust, dirt, scale, etc.) is found within the valve body or mechanism. Re- place the valve.
DO NOT install relief devices in series or backwards. USE CARE when working near or in line with a compressed spring. Sudden release of the spring can cause it and objects in its path to act as projectiles. DO NOT STEP on refrigerant lines. Broken lines can whip about and release refrigerant, causing personal injury. DO NOT climb over a machine. Use platform, catwalk, or staging.
Follow safe practices when using ladders. USE MECHANICAL EQUIPMENT (crane, hoist, etc.) to lift or move inspection covers or other heavy components. Even if com- ponents are light, use mechanical equipment when there is a risk of slipping or losing your balance. BE AWARE that certain automatic start arrangements CAN ENGAGE THE STARTER, TOWER FAN, OR PUMPS. Open the disconnect ahead of the starter, tower fan and pumps. Shut off the machine or pump before servicing equipment. USE only repaired or replacement parts that meet the code require- ments of the original equipment.
DO NOT VENT OR DRAIN waterboxes containing industrial brines, liquid, gases, or semisolids without the permission of your process control group. DO NOT LOOSEN waterbox cover bolts until the waterbox has been completely drained. DOUBLE-CHECK that coupling nut wrenches, dial indicators, or other items have been removed before rotating any shafts. DO NOT LOOSEN a packing gland nut before checking that the nut has a positive thread engagement.
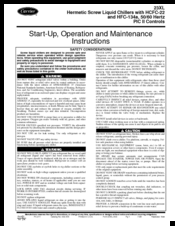
PERIODICALLY INSPECT all valves, fittings, and piping for cor- rosion, rust, leaks, or damage. PROVIDE A DRAIN connection in the vent line near each pres- sure relief device to prevent a build-up of condensate or rain water. 23XL 50/60 Hz Hermetic Screw Liquid Chillers With HCFC-22 and HFC-134a Manufacturer reserves the right to discontinue, or change at any time, specifications or designs without notice and without incurring obligations. Book 2 Tab 5e PC 211 Catalog No.
Carrier 23xl Service Manual
532-303 Printed in U.S.A. Form 23XL-2SI Pg 1 9-94 Replaces: 23XL-1SI.
. Cookie Consent We use cookies to improve your website experience. To learn about our use of cookies and how you can manage your cookie settings, please see our. By continuing to use the website, you consent to our use of cookies.
Welcome to HVAC-Talk.com, a non-DIY site and the ultimate Source for HVAC Information & Knowledge Sharing for the industry professional! Here you can join over 150,000 HVAC Professionals & enthusiasts from around the world discussing all things related to HVAC/R. You are currently viewing as a NON-REGISTERED guest which gives you limited access to view discussions To gain full access to our forums you must; for a free account. As a registered Guest you will be able to:.
Participate in over 40 different forums and search/browse from nearly 3 million posts. Post photos, respond to polls and access other special features.
Gain access to our free AOP (Ask a Professional) Section to get real answers for your questions. All this and much more is available to you absolutely free when you; for an account, so today! We suggest not registering using an AT&T, BellSouth, AOL or Yahoo email address. If you have any problems with the registration process or your account login, please. I did a search before posting this but didn't find anything - We have a 225 ton Carrier 23XL chiller. It was installed new about 1996 when it replaced one of two 175 ton Carrier 19DG chillers. It has had all kinds of problems including major overhauls every 2-3 years.
Several of these overhauls were due to the slide valve failing in some way and taking out major components. By comparison, the remaining 31 year old 19DG chiller has been very reliable. We now have Carrier as our service provider. The 23XL will shut down on a regular basis on low oil level. The oil is not returning properly.
Adding oil only helps the problem for a short time as the new oil doesn't return either. We can keep the 23XL running by running the 19DG at the same time so the 23XL doesn't load up very much. But - for the moment - 175 ton 19DG is carrying the load. So we are only running the 19 DG. Carrier is telling us they don't know why there is an oil return problem. They suspect something major like the slide valve is getting ready to fail again. Their recommendation - replace the chiller!
I don't work on the chiller everyday - I only get called in when there is trouble (I'm the commissioning agent for the Owner). Way back when the 23XL was installed I think I remember there were oil return problems due to low condenser water temperature (below 80 degrees). We lowered the condenser water setpoint to 78 on Carrier's suggestion when we switched to the 19DG last fall. When we tried to bring the 23XL on line for the summer we couldn't keep it on line.
But we never raised the condenser water setpoint. Has anybody seen this before? Is that something that our local Carrier office should know about? It seems that a 2 degree condenser water change is pretty particular to stop a chiller from running.
Any other suggestions for an oil return problem? Now if it is true that the unit shuts down so much and is costing you money and is an ongoing issue why not call in carriers engineers? We took on a bad account 1 time after a previous contractor screwed up so there had been so many problems that we ended up having carriers big shots come out. 1 guy even flew out to the site.
Probation and parole civil service study guide. PAROLE OFFICER I. STUDY GUIDE/SAMPLE TEST. Meeting the job requirements for Probation and Parole Officer (see job. Read the questions and all of the choices carefully. Field when they evaluate and refer offenders for services.
Carrier wants your money so usually they will bend over to help find the problem. You could say hey we figure on replacing the unit in 2-3 yrs and we are thinking about using trane and see how they handle that. I have had positive experience with carrier and if there is an issue with the equipment they will resolve it.
If there is a problem with the installation I would resolve that first. The simple answer is yes, Carrier should know how to solve your problem. If the compressor is on it's way out then of course they are going to suggest replacing the chiller because their own 'Hayden' replacement is ridiculously over priced.
Carrier Chiller Parts
I have no problem working in Austin if the money is right. But, I could probably hook you up with someone in the area that can help you.
You should contact me directly if you want some real help. I will tell you that I just completed a job where I replaced the 'Ingersol Rand' compressor on a 23XL with a competitor (Not Hayden) & I replaced the controls & added a soft starter all for less than half of what a replacement chiller would cost & for about half of what the Hayden/Carrier replacement would cost. Having said that, I can afford to send someone to you.
But, lets think about oil loss for a minute. This time of the year it should not be much of an issue. You can try an oil sample & maybe even a vibe analysis (if you are into voo doo) & maybe something will show up there that may help determine that there is an internal problem.
Most of the time, somebody has to go inside & take a look around. You have options, but you won't hear about them from the OEM. BTW, post a pic of the work horse (19DG). They are great machines & for the record, 30 years is not really that old for a centrifugal. Might mean its inefficient but thats about all.
Replacing the other 19DG with a 23XL was a mistake in my mind. But, screws were the rage some years back because of first cost. But, lets think about oil loss for a minute.
This time of the year it should not be much of an issue. You can try an oil sample & maybe even a vibe analysis (if you are into voo doo) & maybe something will show up there that may help determine that there is an internal problem.
Most of the time, somebody has to go inside & take a look around.This installation is on a museum so down time is critical. Add that budgets are non-existent at the moment.
I don't think vibe analysis is going to show much without a baseline. Oil sample might provide a little more info. A tear down would be the best option but I'm still questioning if it is needed. You have options, but you won't hear about them from the OEM. BTW, post a pic of the work horse (19DG). They are great machines & for the record, 30 years is not really that old for a centrifugal. Might mean its inefficient but thats about all.
Replacing the other 19DG with a 23XL was a mistake in my mind. But, screws were the rage some years back because of first cost.I get a picture to post but it will be next week before I am back at that site.
The other 19DG was replaced for 'other reasons'. Two buildings were being combined onto one central plant so it was thought that the 175 ton chiller wasn't big enough. (Current operation shows that it is.) Since it had to be increased, we got additional funding to go with the 'higher efficiency' screw chiller. We have had so many problems with the 23XL we have regretted replacing the 19DG ever since. Piecing together the modle number from the info I have with me - 23XL2020NC51. Note this from documents like the TAB report - not off the machine itself.
This is an R22 unit with POE oil. If you have an economizer you should have 750LBS R22. If no economizer you should have 700LBS R22. You'll most likely notice on the chiller name plate factory charge specification is greater than the above figures. The above is the correct charge you should have. If it's a frame 1-2 your oil charge should be 4.2 gallons, frame 4 it should be 10 gallons.
Carrier Chillers Specifications
Run the machine at high load, recover that oil as much as you can. Then take the time and weigh your charge and I'll bet it's over charged, including your oil. If and when you take the gas out be sure you change the flared oil strainers, oil filter and always be sure you shut of the oil heater before taking the oil out.
What was the reason for upsizing the 23XL from the old DG? Nevermind I must have missed it.There was an additional 76,176 square feet added to the load. That additional square footage is an historic building which houses historical archives material and therefore must maintain stringent environmental conditions. As far as the machine being over charged.I've kept a pretty close eye on my refrigerant inventory and I don't see how it can be over charged based on that. It is conceivable that our previous service contract holder 'slipped' some 'extra' refrigerant into the machine when I wasn't looking, however its pretty unlikely since I would expect to be charged a premium for ANY materials used.
We are scheduled for our next monthly PM next week and I will put forth this recommendation to the tech.he's pretty knowledgeable and was one of the people involved with the installation of this unit. It has also been suggested that Carrier's engineers take a closer look at our situation but I'm not sure where we are in that process. Thanks for all the responses to this, the input is very appreciated!!! There was an additional 76,176 square feet added to the load. That additional square footage is an historic building which houses historical archives material and therefore must maintain stringent environmental conditions.
As far as the machine being over charged.I've kept a pretty close eye on my refrigerant inventory and I don't see how it can be over charged based on that. It is conceivable that our previous service contract holder 'slipped' some 'extra' refrigerant into the machine when I wasn't looking, however its pretty unlikely since I would expect to be charged a premium for ANY materials used. We are scheduled for our next monthly PM next week and I will put forth this recommendation to the tech.he's pretty knowledgeable and was one of the people involved with the installation of this unit. It has also been suggested that Carrier's engineers take a closer look at our situation but I'm not sure where we are in that process. Thanks for all the responses to this, the input is very appreciated!!!As you say, you've had this problem from the beginning, so an overcharge would not show up as added refgt - it will show up as issues with the machine.
No way to be sure from here that it's an overcharge, but it would be simple enough to pull the liquid and weigh it, and estimate the vapor left in the machine to see how close you are, just to eliminate the possibility. Also the possibility that you have a void in the eliminator screen in the oil separator.
I would check to see what the design tower water is. Usually it is 85 in 95 out.When it falls below 80 degrees the machine usually runs into problems.Also, what type of condenser water valve do you have?is it a mixing valve or just a butterfly valve?These machines like warm tower water.This is actually a concern of mine.I usually set the tower at 78° for the centrifugal and 80° for the screw. The valve is a mixing/balancing valve.I would have to verify the position its in at the moment, but at the same time, to my knowledge, it has not been adjusted. As far as the charge is concerned, the machine has had the slide valve replaced twice.
Both times the charge was completely removed along with the oil, and then weighed back in.but, I personally was not there to verify the charge as it was going in. One other tid bit which may be relevant, this chiller has inlet vanes for lower load conditions.chiller is required to run 24/7 to meet the environmental conditions of the historic building and its archives. So, overnight loads can be very light. I know, there are much more cost effective ways to do what we are doing, but it takes money to begin with and that is a luxury we don't have. As you say, you've had this problem from the beginning, so an overcharge would not show up as added refgt - it will show up as issues with the machine. No way to be sure from here that it's an overcharge, but it would be simple enough to pull the liquid and weigh it, and estimate the vapor left in the machine to see how close you are, just to eliminate the possibility. Also the possibility that you have a void in the eliminator screen in the oil separator.I also like to remove the charge and weigh in.
It really removes alot of doubt and usually the guessing game steers in another direction. Quick Navigation. Site Areas.
Forums.