Vw Golf 1 Gearbox Repair Manual
Selector rod forward 5-speed manual gearboxGearbox 020, up from 1.5 LitreGolf Mk1 / Golf Mk1 convertibleScirocco Mk1 und Mk2Caddy Mk1Jetta MK1. Haynes Publishing is the home of car, motorcycle, scooter and ATV manuals, as well as a range of other specialist topics in print and digital. Renault Clio Petrol & Diesel (Jun 2001. Subscription: 1 year. List Price £20.00.
. VW Golf & Jetta Service and Repair Manual I M Coomber and Christopher Rogers Models covered (1081 - 344 - 1AA11) VW Golf & Jetta Mk 2 models with petrol engines, including fuel injection, catalytic converter, Formel E, 16-valve and special/limited edition models 1043 cc, 1272 cc, 1595 cc & 1781 cc Covers mechanical features of Van. Contents LIVING WITH YOUR VOLKSWAGEN GOLF OR JETTA Introduction Page 0.4 Safety First! Page 0.5 Roadside Repairs Introduction Page 0.6 If your car won’t start Page 0.6 Jump starting Page 0.7 Wheel changing Page 0.8 Identifying leaks Page 0.9 Towing Page 0.9. Contents REPAIRS & OVERHAUL Engine and Associated Systems Engine repair procedures - 1.05 and 1.3 litre - pre August 1985 Page 2A.1 Engine repair procedures - 1.05 and 1.3 litre - post August 1985 Page 2B.1 Engine repair procedures - 1.6 and 1.8 litre 8 valve Page 2C.1 Engine repair procedures - 1.8 litre 16 valve Page 2D.1.
Introduction 0.4 The Mk. II Volkswagen Golf and Jetta range of models was bucket tappets, the Digifant, Digijet and Mono-Jetronic fuel injection introduced in March 1984, revised body and trim features being the systems, the 16-valve engine fitted to the GTi variant, the fully main visual difference to the earlier range of models. Safety first!
0.5 Working on your car can be dangerous. Mains voltage is also dangerous. Make Special hazards This page shows just some of the potential sure that any mains-operated equipment is risks and hazards, with the aim of creating a correctly earthed. Roadside repairs 0.6 The following pages are intended to help in dealing with common roadside emergencies and breakdowns. You will find more detailed fault finding information at the back of the manual, and repair information in the main chapters. If your car won’t start If your car won’t start and the starter motor even though the starter. Roadside repairs 0.7 Jump starting Jump starting will get you out of trouble, but you must correct whatever made the battery go When jump-starting a car using a Make sure that the booster battery is flat in the first place.
Vw Golf Service Manual
There are booster battery, observe the following the same voltage as the discharged three possibilities. Roadside repairs 0.8 Wheel changing Some of the details shown here will vary Warning: Do not change a wheel in a situation where you risk being hit by according to model. For instance, the location another vehicle.
On busy roads, try to stop in a lay-by or a gateway. Be wary of of the spare wheel and jack is not the same on passing traffic while changing the wheel - it is easy to become distracted by all cars. Roadside repairs 0.9 Identifying leaks Puddles on the garage floor or drive, or Warning: Most automotive oils The smell of a fluid leaking obvious wetness under the bonnet or and fluids are poisonous. Wash from the car may provide a underneath the car, suggest a leak that needs them off skin, and change out of clue to what’s leaking. Weekly checks 0.10 Introduction There are some very simple checks which Keeping an eye on tyre condition and If your car develops a brake fluid leak, the need only take a few minutes to carry out, but pressures, will not only help to stop them first time you might know about it is when which could save you a lot of inconvenience wearing out prematurely, but could also save.
Weekly checks 0.11 Engine oil level Before you start 4 Make sure that your car is on level ground. 4 Check the oil level before the car is driven, or at least 5 minutes after the engine has been switched off. If the oil is checked imm- ediately after driving the vehicle, some of the oil will. Weekly checks 0.12 Brake fluid level Warning: Brake fluid can harm your eyes damage painted surfaces, extreme caution when handling and pouring it. Do not use fluid that has been standing open for some time, as it absorbs moisture from the air, which can cause a The “MAX”. Weekly checks 0.13 Screen/headlamp washer fluid level Screenwash additives not only keep the weather - which is when you are likely to need it freeze during cold weather. On no account use winscreen clean during foul weather, they also most.
Don’t top up using plain water as the coolant antifreeze in the washer system - prevent the washer system freezing in cold screenwash will become too diluted, and will. Weekly checks 0.14 Tyre condition and pressure the tyre has been punctured, refit the nail so New tyres should be balanced when they are It is very important that tyres are in good fitted, but it may become necessary to re- condition, and at the correct pressure - having that its point of penetration is marked. Weekly checks 0.15 Battery Caution: Before carrying out any work on the vehicle battery, read the precautions given in 'Safety first' at the start of this manual. 4 Make sure that the battery tray is in good condition, and that the clamp is tight. Corrosion on the tray, retaining clamp and the battery itself can be removed with a solution of water and baking soda. Lubricants and fluids 0.16 Lubricants and fluids Component or system Lubricant or fluid Engine.Multigrade engine oil to viscosity SAE 15W/50 or 20W/50 Duckhams QXR, QS, Hypergrade Plus or Hypergrade Cooling system.
Capacities and tyre pressures 0.17 Capacities Component or system Capacity Engine: 1.05 & 1.3 litre: rocker-finger type.3.0 litres with filter change 2.5 litres without filter change hydraulic tappet type. Notes 0.18.
1.1 Chapter 1 Routine maintenance and servicing Contents Air cleaner element renewal. 32 Fuel filter renewal.
2B.1 Chapter 2 Part B: Engine repair procedures - 1.05 and 1.3 litre post August 1985 The following information is a revision of, or supplementary to, that contained in Part A of this Chapter Contents Camshaft - examination.8 Engine - adjustments after major overhaul. 2B.2 Engine repair procedures - 1.05 and 1.3 litre post August 1985 Lubrication system Pump gear teeth backlash: New. 0.05 mm Wear limit.

Engine repair procedures - 1.05 and 1.3 litre post August 1985 2B.3 4 Loosen the coolant pump retaining bolts, job best left to a VW dealer or engine overhaul then turn the pump body clockwise to release specialist. The tension from the timing belt. Remove the 2 Similarly, if the head is warped, its surfaces timing belt from the camshaft sprocket. 2B.4 Engine repair procedures - 1.05 and 1.3 litre post August 1985 7.4 Oil pump components 1 Oil pump 4 Cover 2 Chain 5 Oil seal 3 Gasket 6 TDC bracket 5.17 A valve stem oil seal 18 With the seals removed, the lower spring seats can also be lifted out for cleaning. Engine repair procedures - 1.05 and 1.3 litre post August 1985 2B.5 9.1 Checking oil pump drive chain tension 10.2 Refitting the camshaft 8 Refit the Woodruff key into its slot in the 9 Oil pump - refitting 10 Camshaft - refitting camshaft, where applicable.
2B.6 Engine repair procedures - 1.05 and 1.3 litre post August 1985 11.2a Fitting a new inlet manifold gasket 11.2b Fitting inlet manifold complete with 11.3 Refitting oil pressure switch carburettor 3 If they have been removed, refit the oil 5 Refit the coolant hoses, ensuring that they cylinder head (see illustration). Engine repair procedures - 1.05 and 1.3 litre post August 1985 2B.7 11.13 Cylinder head gasket in position 11.17 Plastic oil shield correctly located 11.18 Locating dowel for valve cover gasket (arrowed) guide the cylinder head into position but this 21 Connect up the exhaust downpipe and 12 Hydraulic bucket tappets - can be done using suitable sized rods. 2B.8 Engine repair procedures - 1.05 and 1.3 litre post August 1985 7 Press the tappet down using a wooden or plastic wedge (see illustration). 8 If free travel of the tappet exceeds that specified, the tappet must be renewed. 13 Engine - adjustments after major overhaul If the valve tappets have been renewed, it is. 2A.1 Chapter 2 Part A: Engine repair procedures - 1.05 and 1.3 litre pre August 1985 Contents Camshaft - examination and renovation. 27 Flywheel - examination and renovation.
2A.2 Engine repair procedures - 1.05 and 1.3 litre pre August 1985 Crankshaft Main journal: Standard diameter.54.0 mm Undersizes. Engine repair procedures - 1.05 and 1.3 litre pre August 1985 2A.3 1.3 litre: Inlet opens.3°. 2A.4 Engine repair procedures - 1.05 and 1.3 litre pre August 1985 block, connected to the air cleaner by a 2 A hoist of 150 kg capacity will be needed to 7 Identify the fuel supply and return hoses rubber hose. Vacuum from the air cleaner lift the engine approximately 1 metre. Engine repair procedures - 1.05 and 1.3 litre pre August 1985 2A.5 5.18 Shift rod coupling screw 5.21 Reversing light switch 5.23 Engine lifting eye difficulty is experienced, it may be necessary to heat up the coupling with a blowlamp whilst observing the necessary fire precautions.
2A.6 Engine repair procedures - 1.05 and 1.3 litre pre August 1985 6.3 Starter motor and exhaust support 6.6a Undo securing bolts (recessed bolt 6.6b. Then separate engine and bracket shown). Transmission 3 Because the rear bearing of the starter 7 Engine dismantling - general 8 Engine ancillary components armature is in the bellhousing, it is necessary. Engine repair procedures - 1.05 and 1.3 litre pre August 1985 2A.7 9 Cylinder head - removal 1 If the engine is still in the vehicle, first carry out the following operations: a) Disconnect the battery negative lead b) Remove the air cleaner and fuel pump c) Drain the cooling system and remove the top hose and thermostat d) Remove the distributor and spark plugs. 2A.8 Engine repair procedures - 1.05 and 1.3 litre pre August 1985 10.7 Removing oil spray tube 10.8 Removing a cam follower clip 10.9 Removing a cam follower crankshaft pulley is aligned with the TDC 9 Identify each cam follower for location then 10 Camshaft - removal pointer on the front of the oil pump.
Engine repair procedures - 1.05 and 1.3 litre pre August 1985 2A.9 11.2a Compressing a valve spring to remove split collets 11.2b Removing valve springs and retainers. 11 Scrape away all carbon from the valve 8 Examine the valve heads for pitting and 11 Cylinder head - dismantling burning.
2A.10 Engine repair procedures - 1.05 and 1.3 litre pre August 1985 13 If possible, compare the length of the valve springs with new ones and renew them as a set if any are shorter. 14 If the engine is still in the vehicle, clean the piston crowns and cylinder bore upper edges but make sure that no carbon drops between the pistons and bores. Engine repair procedures - 1.05 and 1.3 litre pre August 1985 2A.11 14.13a Withdrawing crankshaft rear oil 14.13b. And gasket 14.14 Remove crankshaft rear oil seal seal housing. From housing 14 Support the housing and drive out the oil a) Jack up the front of the vehicle and 16 Oil pump - removal seal (see illustration). 2A.12 Engine repair procedures - 1.05 and 1.3 litre pre August 1985 17.4 Checking connecting rod endfloat 17.5 Piston crown showing arrow which 17.7 Withdrawing a big-end cap points to timing belt end of engine and repeat the procedure on No 2 and 3 17 Pistons and connecting rods pistons.
Engine repair procedures - 1.05 and 1.3 litre pre August 1985 2A.13 21 Crankshaft and bearings - examination and renovation 1 Examine the bearing surfaces of the crankshaft for scratches or scoring. Using a micrometer, check each journal and crankpin for ovality. 2A.14 Engine repair procedures - 1.05 and 1.3 litre pre August 1985 24.1a Unscrew relief valve plug. And remove spring and plunger 24.2 Removing oil pump cover. And rotors 24.3b Outer rotor indentation (arrowed) must face cover 4 Clean the components in paraffin and wipe.
Engine repair procedures - 1.05 and 1.3 litre pre August 1985 2A.15 29.2 Fitting centre main bearing shell 29.3 Thrustwasher location on centre 29.4 Fitting centre main bearing cap main bearing 4 Lower the crankshaft into position, then fit hammer and at the same time, guide the 29 Crankshaft and main the main bearing caps in their previously connecting rod into the crankpin. 2A.16 Engine repair procedures - 1.05 and 1.3 litre pre August 1985 can be replaced by socket-headed bolts to facilitate their removal with the engine in the vehicle.
Note that the tightening torque for the replacement bolts is 8 Nm (6 Ibf ft). 4 If the engine is in the vehicle, replenish it with oil, fasten the alternator wire to the sump clip and lower the vehicle to the ground. Engine repair procedures - 1.05 and 1.3 litre pre August 1985 2A.17 16 Press the oil spray tube into the top of the cylinder head. 17 Refit the valve cover with a new gasket, locate the reinforcement strips and tighten the nuts and bolts. 2A.18 Engine repair procedures - 1.05 and 1.3 litre pre August 1985 c) Adjust the clutch 37 Timing belt and sprockets - 38 Valve clearances - checking d) Adjust the accelerator cable and, where refitting and adjustment applicable, the choke cable e) Refill the engine with oil and coolant 1 Fit the Woodruff key in the crankshaft and 1 The valve clearances can be checked.
Servicing specifications 1.2 Lubricants, fluids and capacities Refer to the end of “Weekly checks” Engine Oil filter.Champion C101/C160 Valve clearances 1.05 and 1.3 litre engines - pre August 1985. Servicing specifications 1.3 CO content (%) 1.05 litre carburettor engines: Pierburg/Solex 31 PIC-7.0.5 to 1.5 Pierburg/Solex 1B3 and Weber 32 TLA.
Servicing specifications 1.4 Charging system Alternator drivebelt tension Initial adjustment for new drivebelt.2.0 mm deflection under finger pressure at point midway between alternator and crankshaft pulleys Adjustment after 500 miles (750 km). Maintenance schedule 1.5 The maintenance intervals in this Manual wish to perform some of these procedures speeds (idling in traffic) or on short journeys, are provided with the assumption that you will more often. Encourage frequent then more frequent maintenance intervals are be carrying out the work yourself.
Maintenance schedule 1.6 Vehicles manufactured after August 1985 Every 250 miles (400 km) or weekly Every 10 000 miles (15 000 km) - if completing more than 10 000 miles See “Weekly checks” (15 000 km) per annum Every 1000 miles (1500 km) Renew engine oil and filter (Section 18) Check brake pad linings (Section 26) or monthly. Maintenance - component location 1.7 Underbonnet view – 1.3 litre model (air cleaner removed) 1 Engine oil dipstick 2 Fuel line filter 3 Brake master cylinder reservoir 4 Carburettor 5 Ignition coil 6 Cooling system expansion tank 7 Windscreen/headlight washer reservoir 8 Ignition distributor 9 Battery 10 Cooling fan. Maintenance - component location 1.8 Front underbody view - 1.3 litre model 1 Alternator 2 Oil filter 3 Driveshaft 4 Front mounting 5 Cooling system bottom hose 6 Gearbox 7 Track control arm 8 Tie-rod 9 Exhaust 10 Engine sump Front underbody view - fuel injected model 1 Driveshaft 2 Front mounting.
Vw Golf Manual Transmission
Maintenance - component location 1.9 Rear underbody view - 1.3 litre model 1 Exhaust 2 Fuel tank 3 Rear shock absorber lower mounting 4 Axle beam 5 Handbrake cable (right- hand) 6 Handbrake cable (left-hand) 7 Rear drum brake Rear underbody view - fuel injected model 1 Exhaust 2 Fuel tank 3 Rear shock absorber lower. Maintenance procedures 1.10 first step this maintenance engine wear, conventional maintenance as 1 Introduction programme is to prepare yourself before the described in this Chapter will not greatly actual work begins. Read through all the improve the performance of the engine, and Sections relevant to the work to be carried may prove a waste of time and money, unless out, then make a list and gather together all. Every 1000 miles or monthly 1.11 covered.
On some batteries the case is 6 Fluid leakage and engine translucent and incorporates MINIMUM and electrical system check MAXIMUM level marks. The check should be made more often if the vehicle is operated in high ambient temperature conditions. Maintenance procedures 1.12 11.1 Disconnect LT lead (A) earth strap (B) 11.2 Withdraw distributor cap and screen 11.3 Pull off the rotor arm and release securing clips (C) ring Every 5000 miles (7500 km) or 6 months from the distributor (see illustration). 11 Contact breaker point check 3 Pull off the rotor arm and remove the dust cover (see illustration).
Every 10 000 miles or 12 months 1.13 9 The engine will turn over more easily if the adjustment should give a deflection of 2.0 mm. Spark plugs are removed. Do not rotate the After a suitable running in period of about 500 engine by turning the camshaft sprocket as miles (750 km), belt adjustment should be rechecked and adjusted to deflect 5.0 mm. Every 10 000 miles or 12 months 1.14 14 Antifreeze concentration check Warning: Wait until the engine is cold before checking antifreeze. Do not allow antifreeze to come in contact with your skin or painted surfaces of the vehicle. Rinse off spills immediately with plenty of water.
Every 10 000 miles or 12 months 1.15 16.10b Adjusting contact breaker points gap 16.10c Two pips and notch (arrowed) for inserting screwdriver when adjusting contact breaker points gap 5 Connect a 12 volt test bulb between the coil 13 Wipe clean the distributor cap and make used with a special VW tester to give an sure that the carbon brush moves freely instant read-out. Every 10 000 miles or 12 months 1.16 17.17 Ignition timing marks A 1.05 and 1.3 litre B 1.6 and 1.8 litre (carburettor models) C 1.8 litre (fuel injection models) 17.34 Disconnecting temperature sender wire 15 Connect a tachometer in accordance with 27 Point the timing light at the timing mark retighten to 20 Nm (15 Ibf ft) and repeat the the manufacturer’s instructions. Every 10 000 miles or 12 months 1.17 18.13 Using a chain wrench to unscrew oil 19.2 Check exhaust system connections 19.3 Check exhaust system mountings filter for leaks and security the oil filter, as described below, while the oil 16 On completion, replenish the engine oil 2 If excessive effort is required to operate the is draining.
Every 10 000 miles or 12 months 1.18 22.4 Gearbox filler/level plug location 22.10 Using a key to unscrew level plug - (arrowed) - 084 gearbox 020 5-speed gearbox 4 Wipe clean the area around the filler/level 10 When checking the oil level with the plug, then unscrew the plug and clean it. Every 10 000 miles or 12 months 1.19 25.3a Bend each brake hose to check for 25.3b Check all pipe retaining clips for 26.1 Check brake pad lining wear by cracks security viewing through inspection aperture 3 Switch on the main beam and check that 25 Fuel and brake line, hose 26 Brake pad and rear shoe the areas of maximum illumination coincide.
Every 10 000 miles or 12 months 1.20 gripping the track rod. If the wheel is now accumulation of oily grime from beneath a vehicle. Rocked, movement will be felt at the inner joint 1 Raise the vehicle sufficiently enough to if wear has taken place. Every 20 000 miles or 24 months 1.21 32.7 Air cleaner components - Digijet fuel injection 1 Upper cover 2 Screws 3 O-ring 4 Airflow meter 5 Tamperproof plug 6 Hose clip 7 Intake hose 8 Mixture (CO content) adjusting screw 9 O-ring 32.4b.
3.1 Chapter 3 Cooling, heating and air conditioning systems Contents Air conditioning system compressor - drivebelt adjustment.12 General information and precautions.1 Air conditioning system compressor - removal and refitting. 3.2 Cooling, heating and air conditioning systems Torque wrench settings lbf ft All models Temperature sender unit.Cooling fan thermo-switch.
Cooling, heating and air conditioning systems 3.3 1.0b Cooling system components - 1.05 and 1.3 litre, post August 1985 1 Radiator 5 Cover 9 Automatic choke 13 Camshaft sprocket 2 Fan ring 6 O-ring 10 O-ring 14 Timing belt 3 Expansion tank 7 Thermostat 11 Coolant pump 15 Outer timing cover. 3.4 Cooling, heating and air conditioning systems Air conditioning refrigerant Although the refrigerant is not itself toxic, in the presence of a naked flame (or a lighted cigarette) it forms a highly toxic gas.
Liquid refrigerant spilled on the skin will cause frostbite. Cooling, heating and air conditioning systems 3.5 2.2 Removing expansion tank cap 2.4a Radiator bottom hose connection - 2.4b Radiator bottom hose connection - 1.3 litre 1.8 litre hose and allow the water to circulate through hose in the outlet. Continue flushing until clear the radiator until it runs clear from the bottom water runs from the bottom hose.
3.6 Cooling, heating and air conditioning systems 3.8 Lifting out radiator and cooling fan 3.13 Radiator lower mounting rubber 3.15 Secure fan lead with plastic clip assembly (arrowed) 10 Clean the radiator matrix of flies and small 4 Cooling fan and motor - 5 Thermostat - removal, testing leaves with a soft brush or by hosing. Cooling, heating and air conditioning systems 3.7 5.11a Undo the retaining bolts.
Withdraw thermostat elbow. Then extract thermostat and seal Refitting Refitting Refitting 8 Refitting is a reversal of removal. Fit a new 8 Refitting is a reversal of removal. 3.8 Cooling, heating and air conditioning systems 7.3 Cooling fan thermo-switch 7.11 Temperature sender unit thermo- 7.12 Temperature sensor (arrowed) - switch location - 1.05 and 1.3 litre 1.05 and 1.3 litre the joint. Clean off the old gasket. Cooling fan temperature sensor on the spark plug side of the cylinder head. Cooling, heating and air conditioning systems 3.9 8.3a Pulling free heater/ventilation control 8.3b Unclip and withdraw trim panel 8.4 Detaching control unit knobs 8.6a Removing parcel shelf.
And insulation sheet 8.6c Control cable connections to flap valves at heater distribution box unit necessary to remove the lower parcel tray on a good idea to fit new cable clamps also, as. 3.10 Cooling, heating and air conditioning systems 10.6 Heater and ventilation system components 6 Undo the retaining nuts and withdraw the further coolant drainage from the inlet and faces of the segments (see illustration).
Outlet distributor from box, outlet pipes. Renew the heat exchanger cover gasket and disconnecting the distributor from the left and 10 The housing upper and lower housing. Cooling, heating and air conditioning systems 3.11 2 Place the compressor on the side of the 11 Air conditioning system 12 Air conditioning system engine compartment when removing the compressor - removal and compressor - drivebelt engine and only move it to the point where the refitting flexible refrigerant hoses are in no danger of adjustment. 3.12 Notes 1081 VW Golf & Jetta. 2D.1 Chapter 2 Part D: Engine repair procedures 1.8 litre 16 valve The following information is a revision of, or supplementary to, that given for the 1.8 litre engine in Part C of this Chapter Contents Camshafts - removal and refitting.3 Pistons and connecting rods - removal and refitting.
2D.2 Engine repair procedures 1.8 litre 16 valve 1.0 The 1.8 litre, 16 valve, fuel injection engine 1 Inlet manifold upper section 2 Gasket 3 Valve cover 4 Gasket 5 Cylinder head assembly with camshafts 6 Cylinder head gasket 7 Cylinder block assembly 8 Gasket 9 Sump 10 Oil filter head. Engine repair procedures 1.8 litre 16 valve 2D.3 1 General information The 1.8 litre, 16-valve engine fitted to GTi models from October 1986, incorporates double overhead camshafts, one operating the exhaust valves and the other the inlet valves. There are four valves per cylinder which operate simultaneously in pairs and provide the engine with a much improved breathing capability over the 8-valve version. 2D.4 Engine repair procedures 1.8 litre 16 valve 12 If necessary, remove the hydraulic bucket 20 Refit the exhaust camshaft end caps and 5 Pistons and connecting rods tappets. Check the camshafts and drive chain bearing cap Nos.
1 and 3, then progressively - removal and refitting for wear. 2C.1 Chapter 2 Part C: Engine repair procedures - 1.6 and 1.8 litre 8 valve Contents Camshaft - removal, examination and refitting.10 Intermediate shaft - examination and renovation. 2C.2 Engine repair procedures - 1.6 and 1.8 litre 8 valve Compression pressure: 1.6 litre: New.9 to 12 bar Minimum. Engine repair procedures - 1.6 and 1.8 litre 8 valve 2C.3 Stem diameter: Inlet.
7.97 mm Exhaust. 2C.4 Engine repair procedures - 1.6 and 1.8 litre 8 valve Valve timing (continued) Nil valve clearance at 1.0 mm valve lift 1.8 litre (code RH): Inlet opens.2°. Engine repair procedures - 1.6 and 1.8 litre 8 valve 2C.5 Cylinder head bolts (engine cold).As for 1.05 and 1.3 litre engines Refer to illustration 5.25b. 2C.6 Engine repair procedures - 1.6 and 1.8 litre 8 valve 5.8a Oil pressure switch location in rear of 5.8b Oil pressure switch location in filter 5.8c Earth strap to gearbox cylinder head mounting 5 Remove the radiator, together with the cooling fan. Engine repair procedures - 1.6 and 1.8 litre 8 valve 2C.7 26 The engine/gearbox unit is now ready for lifting out but first make a final check that all cables, wiring and hoses are clear. 27 Have an assistant at hand to help guide the unit clear of the surrounding components in the engine compartment as it is lifted out. 2C.8 Engine repair procedures - 1.6 and 1.8 litre 8 valve I) Coolant pump and coolant hose 6 Engine/gearbox - separation 8 Engine ancillary components connectors from cylinder block and head.
And reconnection - removal New O-rings will be required j) Clutch then intermediate plate (manual gearbox) k) Driveplate, noting location of spacer. Engine repair procedures - 1.6 and 1.8 litre 8 valve 2C.9 9.6 Intermediate sprocket timing mark (arrowed) aligned with 9.7a Camshaft sprocket timing mark (arrowed) with No 1 cylinder notch in crankshaft pulley at TDC on compression face of the cover to allow access to the Allen with the valve cover flange (see illustration). 2C.10 Engine repair procedures - 1.6 and 1.8 litre 8 valve b) If the camshaft oil seal is to be renewed then the camshaft timing sprocket must be removed 2 Remove the camshaft bearing caps (see illustrations), making a careful note of their fitted positions for reference when refitting. Engine repair procedures - 1.6 and 1.8 litre 8 valve 2C.11 and tappet is required. Label the containers 1 4 On carburettor models, remove the air 20 When all ten bolts have been removed, lift to 8, as follows: cleaner unit. The head from the cylinder block.
2C.12 Engine repair procedures - 1.6 and 1.8 litre 8 valve 12.12a Inserting a valve into the cylinder 12.12b Locating valve springs and cap. And valve collets head 4 The valve springs must be renewed if they the straight-edge along the centre of the may be assembled to the valve stem (see are damaged, distorted, or known to have. Engine repair procedures - 1.6 and 1.8 litre 8 valve 2C.13 13.1 Sump, oil pump and oil filter components - fuel injection engine complete with the oil pick-up pipe and 14 Pistons and connecting rods 15 Crankshaft and main strainer. removal bearings - removal Refitting. 2C.14 Engine repair procedures - 1.6 and 1.8 litre 8 valve 15.2 Crankshaft and cylinder block components seen that the caps are numbered 1 to 5 and 5 Lift out the crankshaft and then remove the 3 Remove the fuel pump on carburettor that the number is on the side of the engine top half bearing shells.
Engine repair procedures - 1.6 and 1.8 litre 8 valve 2C.15 2 Carefully prise out the oil seal with a 17 Oil filter - renewal screwdriver or strong wire and wipe clean the recess (see illustration). 3 Fill the space between the lips of the new seal with multi-purpose grease, then drive it squarely into the housing using a block of Refer to Chapter 1, Section 18.
2C.16 Engine repair procedures - 1.6 and 1.8 litre 8 valve 25.2 Examine face of oil pump cover for 25.3 Checking oil pump gear backlash 25.4 Checking oil pump gear endfloat scoring illustration, the gears have marked the cover. 23 Cylinder block/crankcase - 26 Intermediate shaft - If the depth of this marking is significant, then examination and renovation. Davis drug guide amazon.
Engine repair procedures - 1.6 and 1.8 litre 8 valve 2C.17 30.3a Fitting flanged type centre main 30.3b Fitting alternative type centre main 30.3c. Together with thrustwashers bearing into crankcase bearing into crankcase. 30.3d Fitting flanged type centre main 30.3e Fitting centre bearing and separate 30.3f Ensure that ends of bearing are flush bearing to cap.
2C.18 Engine repair procedures - 1.6 and 1.8 litre 8 valve 10 Lubricate the front of the crankshaft and fit the front oil seal and flange with a new gasket. Tighten the bolts to the correct torque.
31 Intermediate shaft - refitting Lubricate the intermediate shaft with clean engine oil then install it in the block. Engine repair procedures - 1.6 and 1.8 litre 8 valve 2C.19 between the camshaft and intermediate shaft 13 Refit the spark plugs, if not already done. 3 Irregular noises are normal when starting sprockets. Tighten the eccentric adjuster nut 14 Refit the gearbox/transmission to the but should become quiet after a few minutes to the specified torque - see illustration 9.8.
2C.20 Notes 1081 VW Golf & Jetta. Maintenance procedures 1.22 Every 30 000 miles (45 000 km) 35 Automatic transmission and final drive fluid renewal Note: Under extreme operating conditions, automatic transmission fluid should be changed at more frequent intervals.
Automatic transmission 1 Whenever the automatic transmission fluid is renewed, the oil pan and strainer must also be cleaned (where applicable). 4A.1 Chapter 4 Part A: Fuel and exhaust systems - carburettor models Contents Accelerator and throttle cables - removal, refitting and adjustment. 10 Choke cable (1.05 litre engine) - removal, refitting and adjustment. 12 Accelerator pedal - removal and refitting. 11 Exhaust system - inspection, removal and refitting. 4A.2 Fuel and exhaust systems - carburettor models Carburettor - 1.05 litre (continued) Pierburg/Solex 1B3 Venturi. 23 mm Main jet.
Fuel and exhaust systems - carburettor models 4A.3 Carburettor-1.6 litre Pierburg/Solex 2E2 - engine code EZ Type. Twin progressive choke, downdraught with automatic choke Stage I Stage II. 4A.4 Fuel and exhaust systems - carburettor models Torque wrench settings (continued) lbf ft 1.6 and 1.8 litre Carburettor.Fuel pump. Fuel and exhaust systems - carburettor models 4A.5 3.6 Air cleaner components – 1.6 and 1.8 litre 1 Warm air deflector plate 2 Gasket 3 Spring washer 4 Nut 5 Air hose 6 Bracket 7 Washer 8 Nut 9 Bonded rubber mounting 10 Clip 11 Air Hose 12 Clip. 4A.6 Fuel and exhaust systems - carburettor models 4.5 Upper view of air temperature sensor - 1.3 litre 5 If the control unit does not operate correctly then renew it, together with the temperature sensor (see illustration). 6 Refit the vacuum unit and inlet pipe. 5 Fuel pump - testing, removal and refitting 5.4a Fuel line attachments –.
Vw Repair Manuals Online
Fuel and exhaust systems - carburettor models 4A.7 3 Lift the floor covering from the luggage 6 Fuel reservoir - removal and compartment then remove the circular sender refitting unit cover (see illustration). 4 Disconnect the wiring plug from the top of the sender unit, also the fuel feed (to pump) and return (from fuel reservoir) hoses. 4A.8 Fuel and exhaust systems - carburettor models 10.3 Accelerator cable to carburettor throttle control 10.4 Release cable grommet from support bracket 9 Have an assistant fully depress the 8 Fuel gauge sender unit - 10 Accelerator and throttle accelerator pedal. Removal and refitting cables - removal, refitting and 10 Check that the clearance between the. Fuel and exhaust systems - carburettor models 4A.9 retaining clip and then disconnect the cable 12 Choke cable (1.05 litre from the carburettor. Engine) - removal, refitting 17 At the transmission end, prise free the securing clip and detach the cable from the and adjustment operating lever and the cable support bracket.
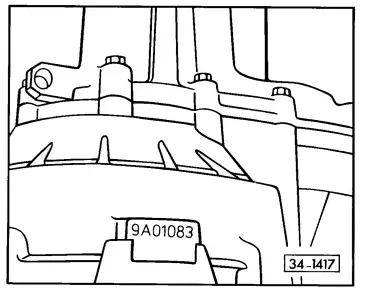
4A.10 Fuel and exhaust systems - carburettor models 13.5a Pierburg/Solex 2E3 carburettor, manifold and associated 13.5b Pierburg/Solex 2E2 carburettor, manifold and associated components components Refitting 11 On completion, top-up the cooling carburettor, check the cost and availability of system, restart the engine and check for fuel spare parts before commencement. Fuel and exhaust systems - carburettor models 4A.11 14.4a Pierburg/Solex PIC carburettor components 1081 VW Golf & Jetta. 4A.12 Fuel and exhaust systems - carburettor models 14.4b Pierburg/Solex 1B3 carburettor top cover components 14.4c Pierburg/Solex 1B3 carburettor main body components 1 Idle speed boost 6 Choke valve 14 Needle valve 1 Bearing ring 8 Fast idle adjustment screw two-way valve 7 Screw 15 Pivot pin. Fuel and exhaust systems - carburettor models 4A.13 14.4e Pierburg/Solex 2E3 carburettor components 14.4f Weber 32 TLA carburettor top cover components 1 Screw 2 Air correction jet 3 Auxiliary fuel jet (if applicable) 4 Idling fuel jet 5 Emulsion tube 6 Choke valve and lever 7 Washer 8 Gauze filter. 4A.14 Fuel and exhaust systems - carburettor models 14.4g Weber 32 TLA carburettor main body components 1 Accelerator pump 2 Injection pipe 3 Part throttle enrichment valve 4 Idle speed boost two-way valve 5 To idle adjusting screw 6 To vacuum line and brake servo 7 Gasket 8 Clip 9 Idle speed adjustment screw. Fuel and exhaust systems - carburettor models 4A.15 15.10 Idle speed (A) and mixture (B) 15.17 Fast idle speed setting 15.20 Enrichment tube adjustment adjusting screw locations A Choke valve held open with rubber band a = 1.0 ± 0.3 mm B Adjustment screw 10 Start the engine and let it idle.